Journal 16
The transition is complete. From a series of sketches to the steel-and-concrete complex which now rises from the Chengdu Plain, the Polestar Production Centre is officially complete. And just as the completion of the Production Centre marks its transformation from theory to reality, so it marks Polestar’s metamorphosis from an idea, that of pure, progressive performance, to a vehicle manufacturer.
Chengdu Inauguration
Hand in hand with the inauguration comes Polestar’s World Manufacturer Identifier (WMI). This designation classifies Polestar as an official standalone car company, truly free to operate as the guiding star of the industry.
The Polestar 1 is where uncompromised design and cutting-edge technology meet. And so is the factory it’s built in. Designed by celebrated Norwegian architecture firm Snøhetta (who are about to add to their already impressive portfolio with the new Shanghai Opera House), the Production Centre embodies the next step in automotive manufacturing. The facility boasts a sweeping curved facade, a universal mezzanine offering unrestricted views of the entire manufacturing process, and a brand experience centre which introduces visitors to the Polestar universe. Like the cars themselves, the production centre is an idea fully realised; true to its initial concept, brought from the page to the real world intact and without compromise.
The Polestar 1 has been designed down to the smallest detail. The way it’s assembled is no different. The Production Centre in Chengdu is host to one of the most exacting and precise manufacturing processes in the automotive industry. From the precision joining of the marriage point (see below) to the hand-detailing of the paint shop, every stage is undertaken by personnel with the same detail-obsessed focus as all other Polestar employees. Their expertise is evident at every stage of the production process.
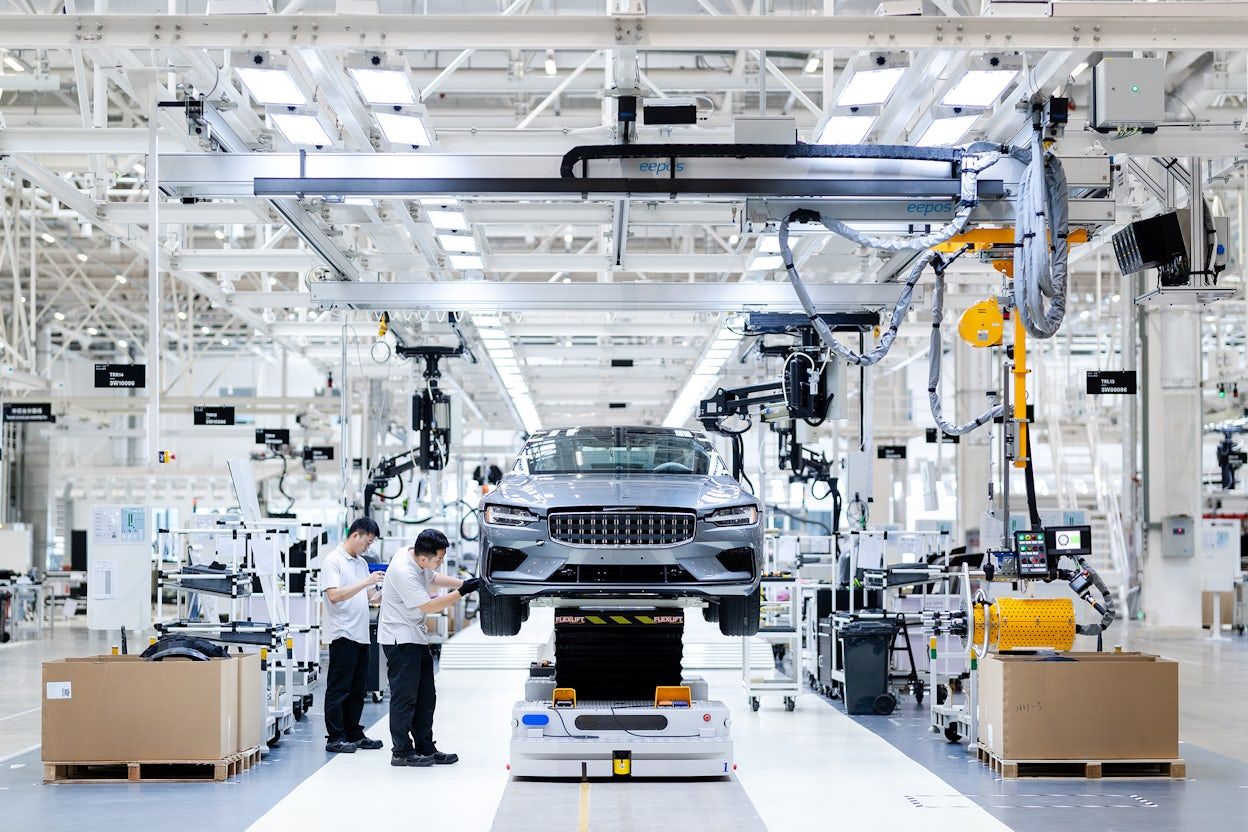
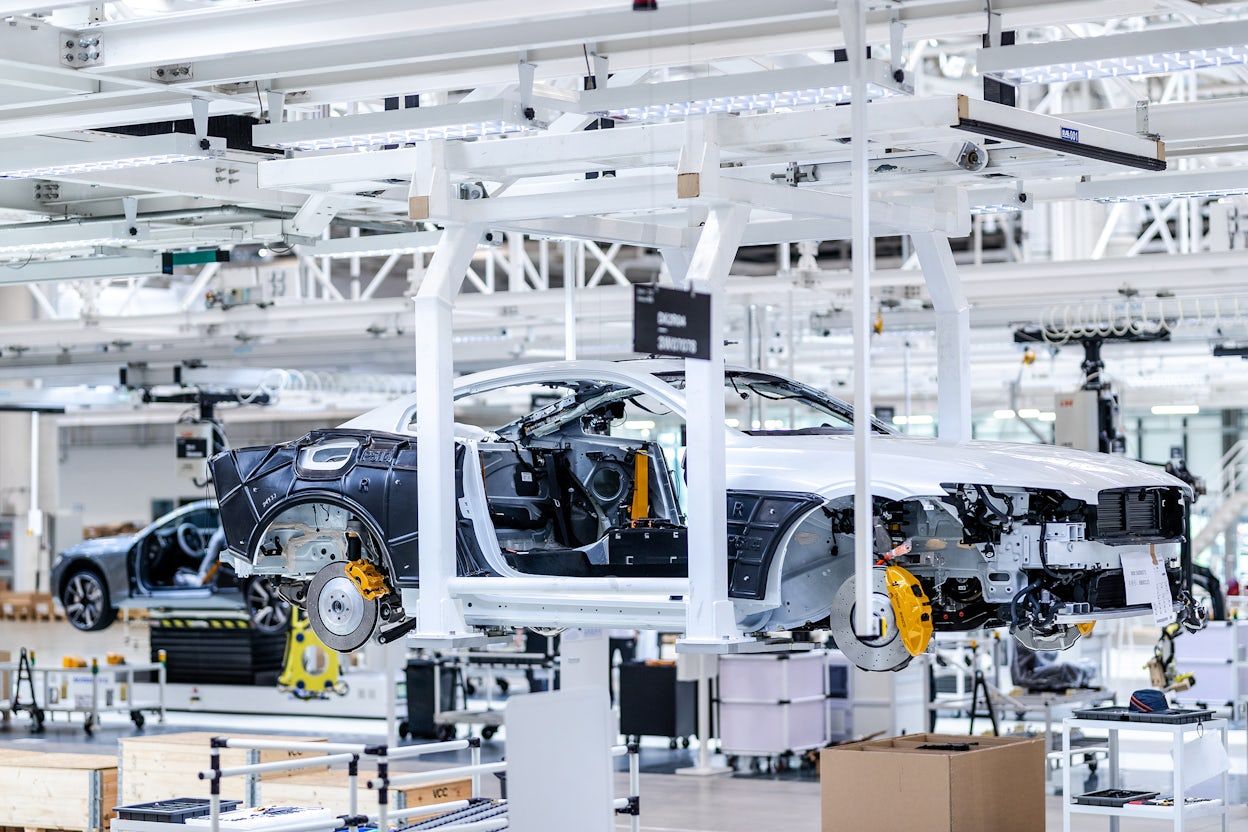
In the assembly shop, where the various components which make up the Polestar 1 come together, things are done by hand: the assembly of the powertrain and transmission, the installation of the interior, and more.
The distinctive carbon fibre body panels of the Polestar 1 are attached to the steel chassis by hand in a specialised jig for absolute precision. Once the body and chassis have become one, the engine, gearbox and suspension are joined with the chassis at the marriage point. Accuracy is key, and each of the bolts protruding from the chassis are perfectly aligned with the body. Once the union is complete, it’s ready for the next stage.
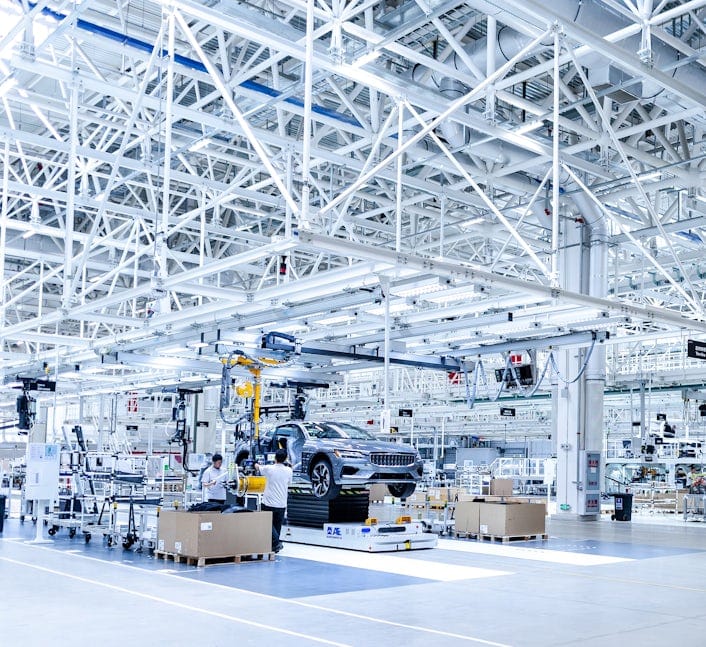
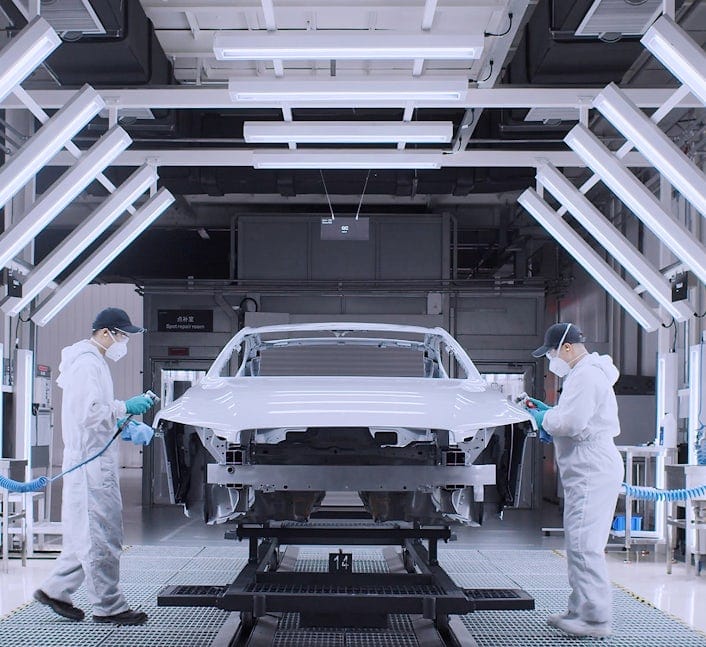
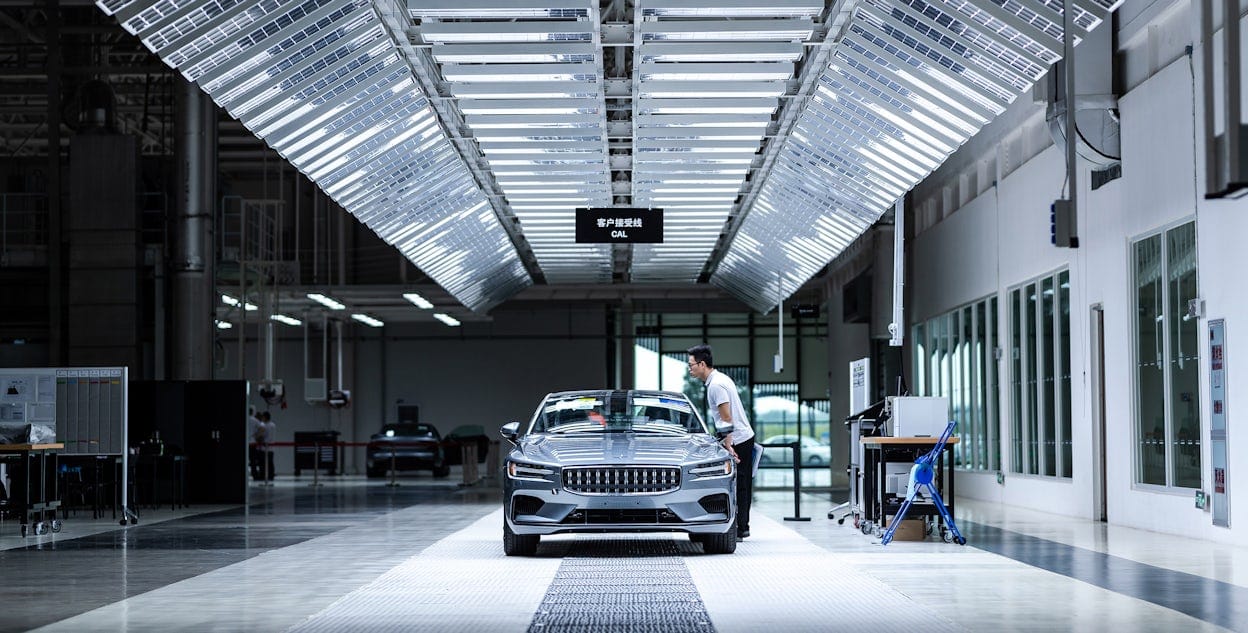
The Polestar 1 then finds itself at a truly unforgiving stage: the Customer Acceptance Line (CAL). This is where a Polestar auditor takes more than eight hours to inspect the car according to “hypercritical sensory standards”, ranging from smell to touch and everything in between.
A focus on sustainability is only natural when guided by the ethos of “pure, progressive performance”. Therefore, the Production Centre was designed with the goal of being one of the most environmentally responsible car manufacturing facilities in China. Aiming for Gold status in LEED (Leadership in Energy and Environmental Design, a globally-recognised rating system), the facility is not only designed with the idea of sustainability at its core, but also committed to only using suppliers which adhere to the strictest environmental standards.
The Polestar Production Centre was also designed to be a physical representation of the brand and its ethos. And for visitors who are unfamiliar with Polestar, there is also the Brand Experience Centre, which presents a curated glimpse into the various aspects of the Polestar universe. Inside the Production Centre itself: a multimedia installation presenting the hardware and engineering of the Polestar 1, along with texts and films showcasing the brand’s identity, design philosophy, and more.
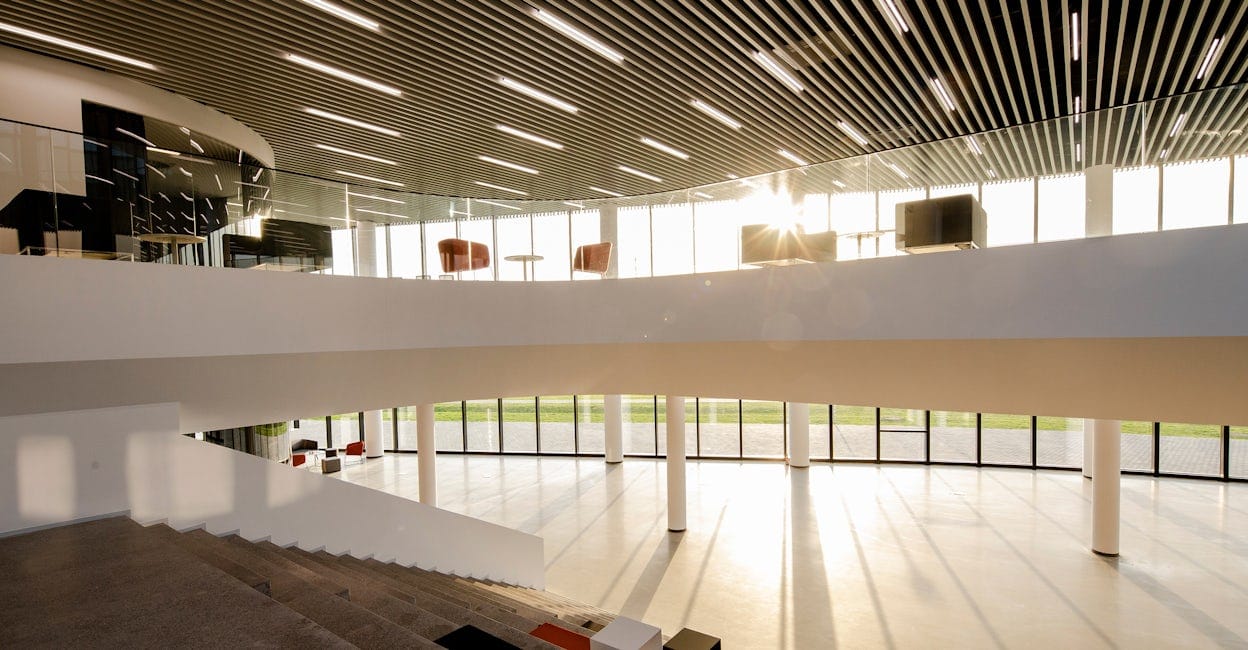
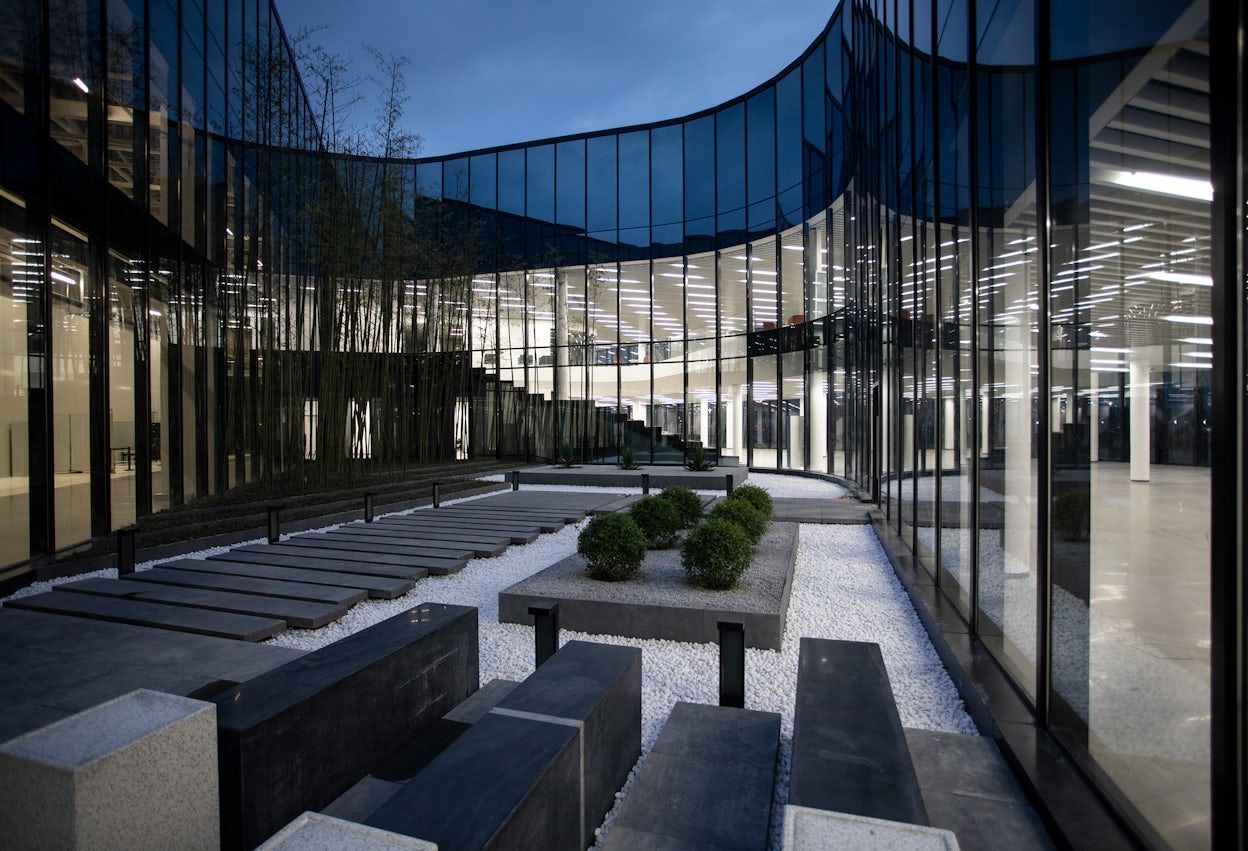
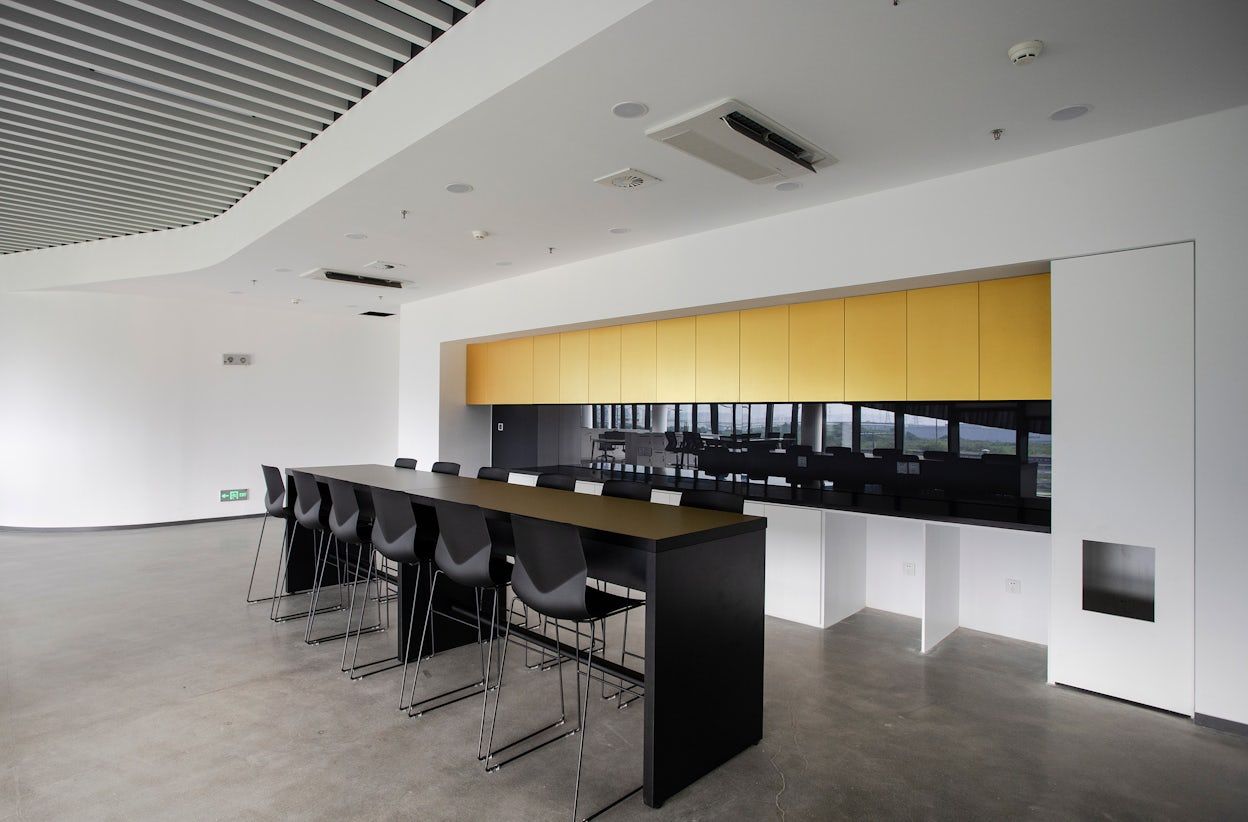
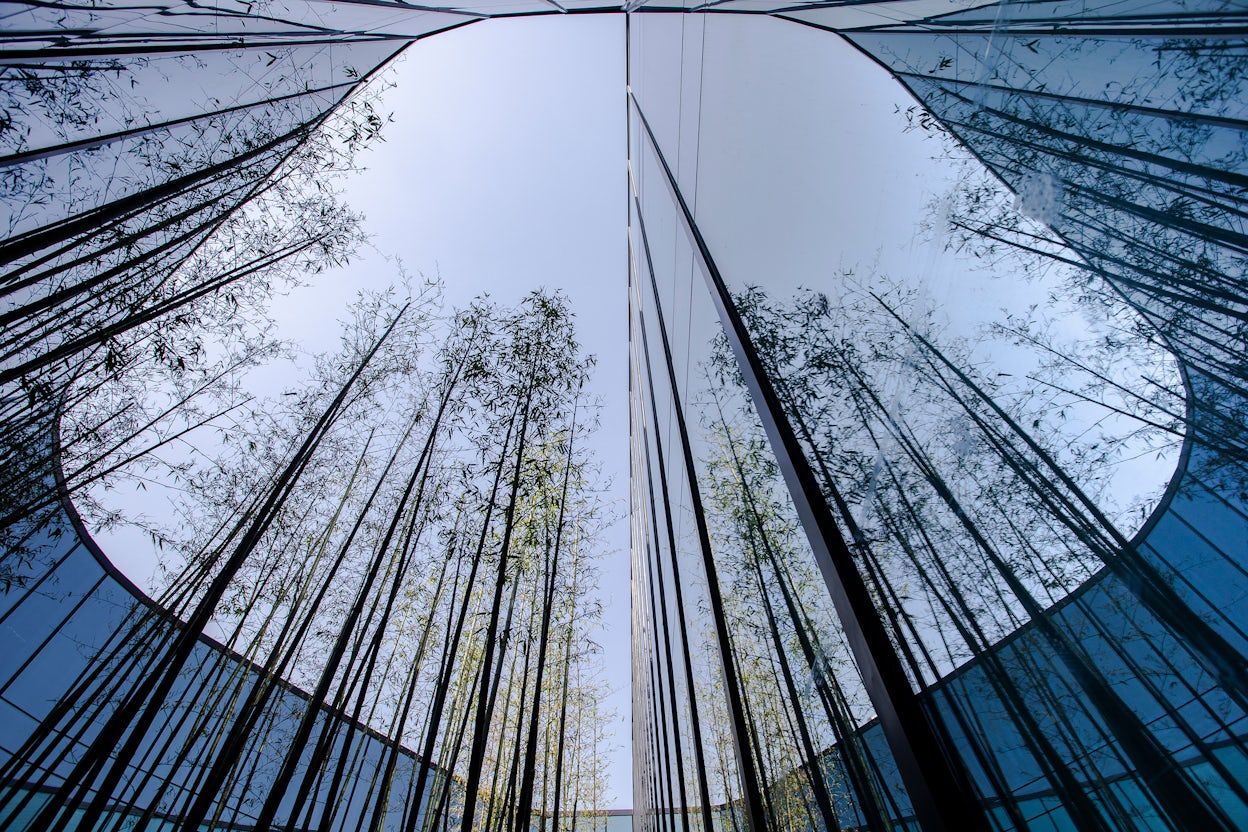
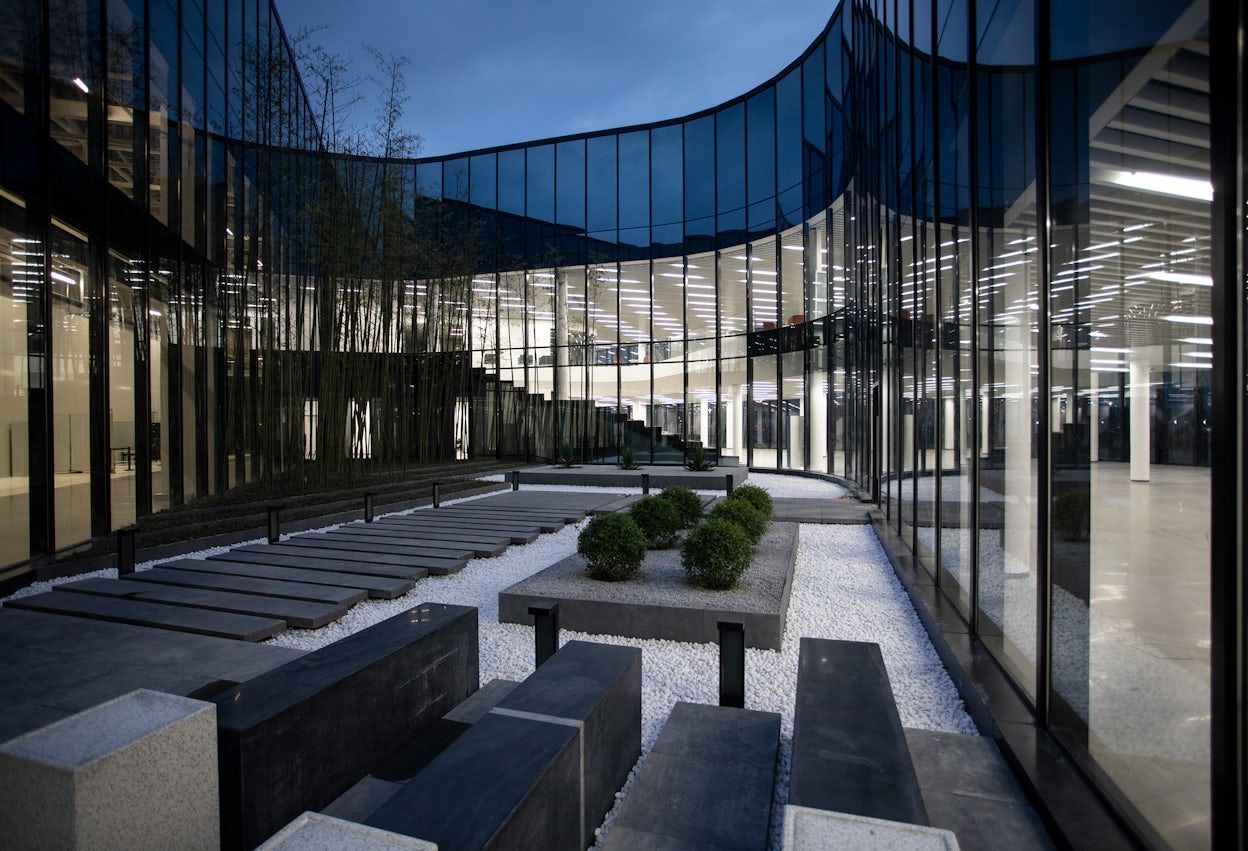
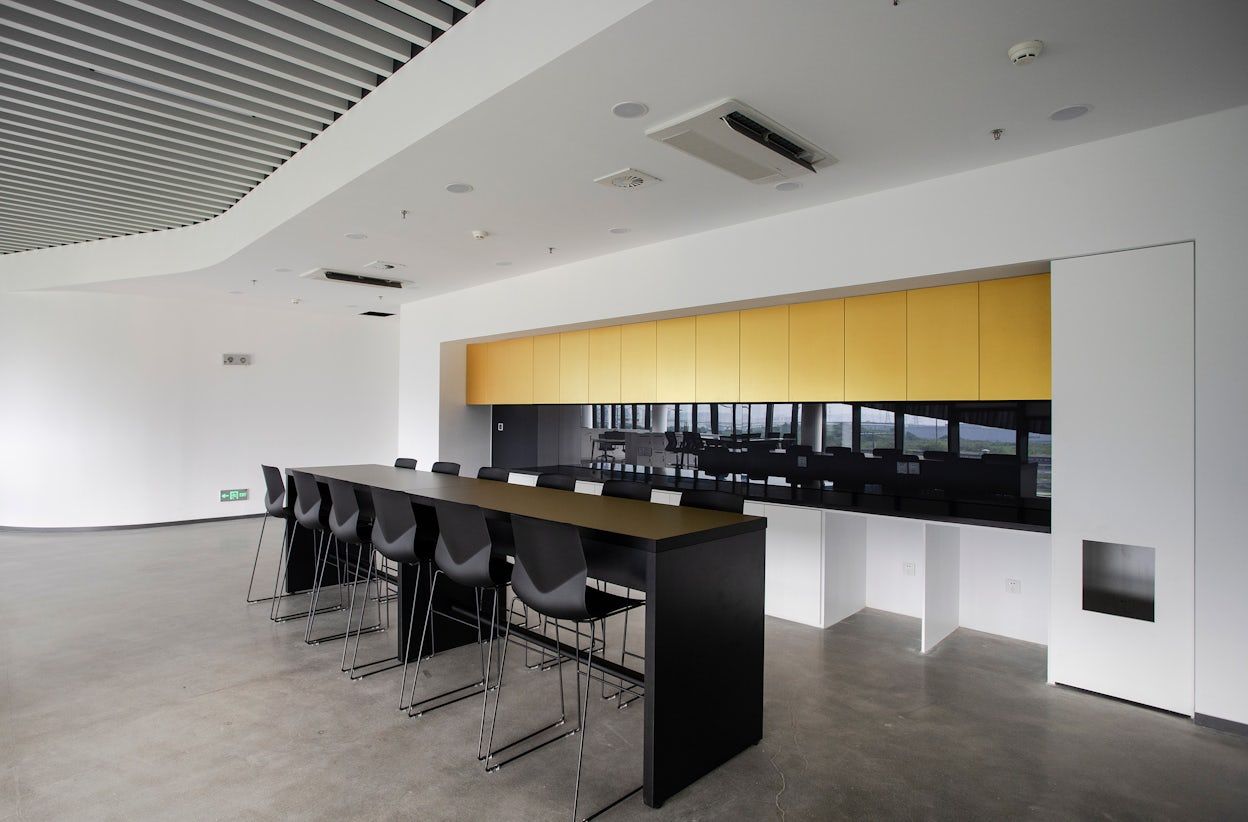
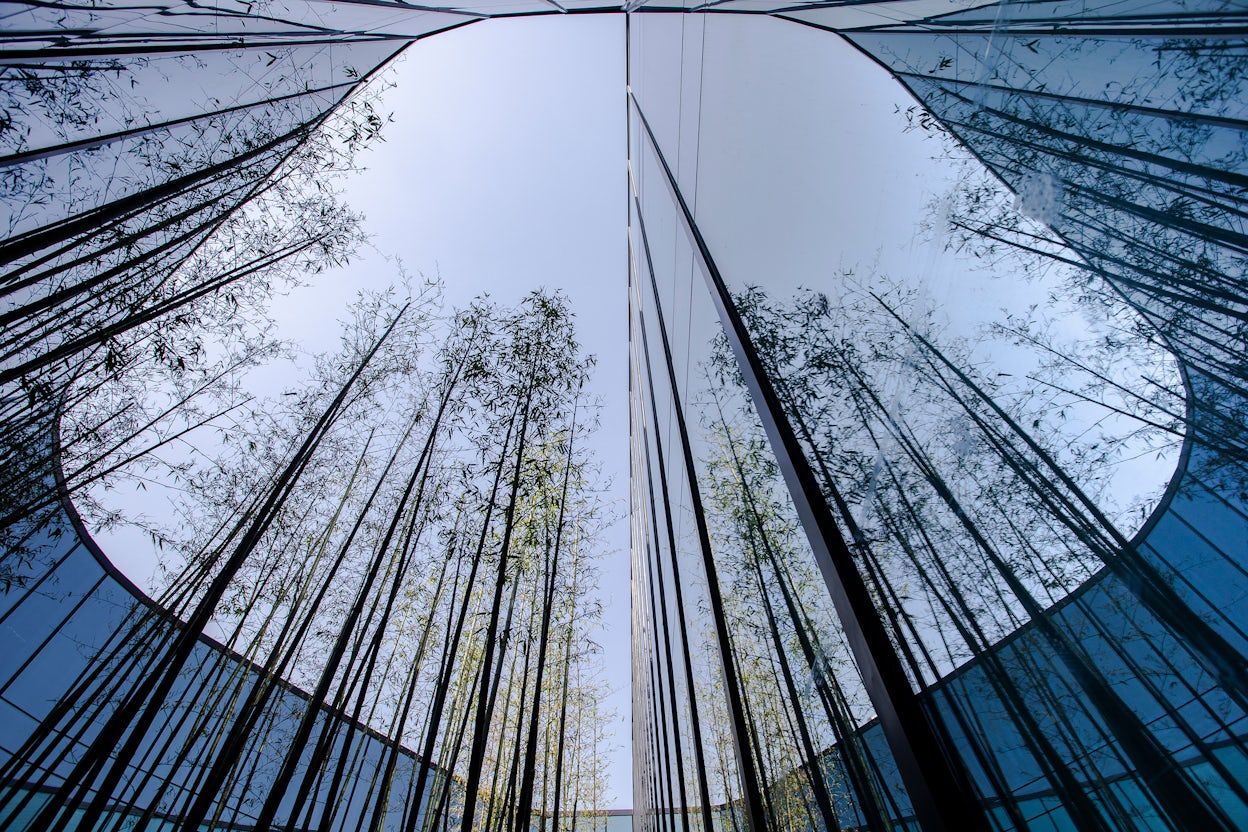
01/03
Polestar was created, in part, to break away from the conventions of the auto industry; to lead by example, to innovate, to show what’s possible when the product is elevated and placed centre-stage. And now, with the Polestar Production Centre complete, these ideas are being realised, in steel and carbon fibre.
The transition is complete.