Journaal 5
Toen de Polestar 1 vorig jaar aan de wereld werd onthuld, waren de reacties overweldigend. Met zijn conceptuele uitstraling liet deze eerste auto van Polestar geen twijfel bestaan. Dit was geen test.

De perfecte balans
Dit was een boeiend nieuw autobedrijf met grote ambities. Iedereen achter de schermen was er vast van overtuigd dat de Polestar – laag, strak en met een opvallend atletische uitstraling – met deze fraaie proporties in 2019 zijn weg naar de allereerste productieversie wel móest vinden.
Maar om trouw te blijven aan het oorspronkelijke ontwerp moesten er geavanceerde materialen worden gebruikt. Koolstofvezel was niet alleen nodig voor het behoud van het slanke postuur en het lage gewicht, maar ook om te kunnen voldoen aan die ambitieuze prestatiedoelstellingen.
Maar hoe lastig zou het materiaal blijken te zijn? Zouden ontwerpers en ingenieurs in staat zijn de juiste materiaalverhouding te vinden? En zouden de voordelen van koolstofvezel werkelijk lonen?
We spraken met Zef van der Putten, Principal Engineer van Polestar 1, om erachter te komen.
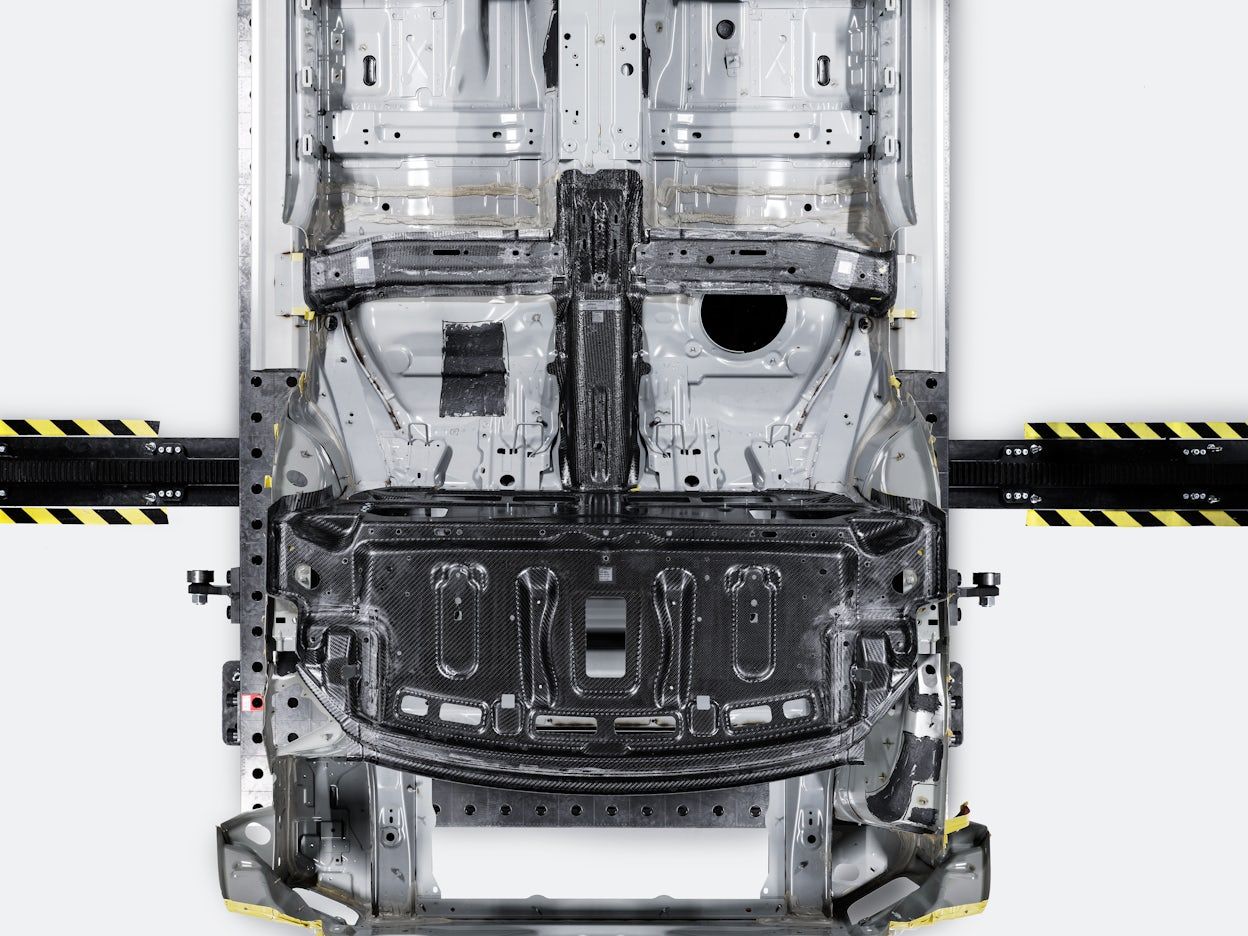
De toepassing van koolstofvezel perfectioneren
Koolstofvezel wordt nog steeds beschouwd als een exclusief, duur en lichtgewicht materiaal, maar daarmee is het de ideale keus voor een auto die zoveel baanbrekende technologie, toekomstgericht denken en prestaties garandeert.
Koolstofvezel deed zo'n dertig jaar geleden haar intrede in de Formule 1. Het was moeilijk om mee te werken, maar had heel wat nuttige eigenschappen en bood talloze voordelen. Wat opviel, was dat het aanzienlijk lichter en sterker was dan andere materialen. Al snel gebruikte elk team het, net als high-end fabrikanten van prestatieauto's – de reputatie van koolstofvezel als serieus prestatieverhogend materiaal was gevestigd.
Vandaag de dag zijn carrosseriestructuren van koolstofvezel het toonbeeld geworden van baanbrekende, high-tech prestaties: minder gewicht, hogere prestaties, een lager zwaartepunt van de auto en een betere torsiestijfheid.
Nadere inspectie van de auto bevestigt dit ook. Wie er een rondje omheen loopt, ontdekt een knap staaltje engineering. De carrosserie, inclusief de deuren, de voorspatborden, de motorkap en het kofferdeksel zijn gemaakt van Carbon-Fibre Reinforced Polymer (CFRP). En dan is er nog die lage daklijn die zoveel mensen in vervoering bracht.
"Met een standaard dakconstructie van staal waren al deze delen groter geweest – het dak hoger en de ramen rechterop. Door de complete dakconstructie van koolstofvezel te maken, was het mogelijk die lage, elegante daklijn te realiseren", aldus Zef.
De libel (Odonata Anisoptera). Het antwoord van de natuur op kracht en wendbaarheid. Gehard door voortdurende evolutie.
Het oog volgt automatisch de lijn van de A-stijl naar de C-stijl. Maar wat niet te zien is, is wat eronder ligt: een uiterst stijve voorgefabriceerde koolstofvezelbuis die ingeklemd ligt tussen twee halve platen van de koolstofvezel stijlconstructie. Die zijn aan de zijkant met elkaar verbonden door smalle, lichte en ultrastijve dwarsprofielen van koolstofvezel.
Maar dat is nog niet alles. Het SPA-chassis is ingrijpend aangepast: we hebben 320 mm van de wielbasis afgehaald en nog eens 200 mm aan de achterkant. Vervolgens heeft de groep, net als alle andere geweldige engineeringteams altijd doen, naar de natuur gekeken voor inspiratie en de 'Dragonfly'* (libel) toegevoegd – een insectvormige lap koolstofvezel die aan het chassis is vastgemaakt. De spanwijdte en het achterlijf zorgen voor een aanzienlijke verbetering van de torsiestijfheid op een van de kritische punten in de carrosseriestructuur tussen de middenvloer en de achterconstructie. Het resultaat is spectaculair: de torsiestijfheid van de chassisconstructie is met 45% toegenomen.
*Een slim vormgegeven patch van CFRP, die is bevestigd aan het stalen onderstel, maakt de traditioneel zwakke interface tussen de middenvloer en de achterconstructie stijver. Bij Polestar is dit onderdeel bekend als de Dragonfly (libel).
Een band opbouwen met het materiaal
Op de vraag hoe het was om in het project met koolstofvezel te werken, zei Zef:
"Een van de voornaamste uitdagingen was het materiaal te leren kennen. Voor de Polestar 1 wilden we de perfecte oplossing en daar hadden we alles voor over. We hebben veel geleerd en ook al ging niet alles precies zoals we hadden verwacht, je leert vaak het meest van de verrassingen. Het proces heeft een zeer hoog niveau van precisie en afwerking opgeleverd."
Toen ze het materiaal eenmaal goed hadden leren kennen, gingen de Polestar-engineers aan de slag met het definiëren en controleren van alle andere parameters. Daarbij moesten cruciale beslissingen worden genomen, zoals welke vezel en welke kunststof te gebruiken, maar ook hoe de verschillende secties te monteren en te spuiten.
Het team heeft ook geleerd het materiaal voor Computer Aided Engineering-berekeningen (CAE) te definiëren, zodat ze de onderdelen konden testen en evalueren. Ze wisten ook uit ervaring dat koolstofvezel zich wisselend gedraagt afhankelijk van de richtinggevende krachten. Dus werden er drapeersimulaties gedaan om te anticiperen op wat het materiaal in werkelijkheid zou doen.
Het voordeel van al die slimme modellen? De richtinggevoelige lagen in het materiaal worden nu specifiek in de auto geplaatst om tegenwicht te bieden aan bepaalde krachten en de weerstand te verhogen onder verschillende rijomstandigheden.
Van de auto verwachtten we grote cijfers in de zin van prestaties en kleine cijfers in de zin van afmetingen en gewicht. Dus hebben we veel research, analyses en tests gedaan en ook zo nu en dan achter onze oren gekrabd. De auto is een indrukwekkende 230 kg lichter dankzij de integratie van het materiaal in het onderstel, waardoor het extra gewicht van de accu's volledig wordt geneutraliseerd.
Indrukwekkend.

Concretiseren van het design
Het concept en de uitvoering van het design zijn voor elk merk van groot belang. Aangezien Polestar 1 de eerste auto was die uit de Polestar-stal kwam, was het cruciaal om een statement te maken en de designtaal van het merk goed te visualiseren.
Volgens Zef speelt het materiaal in eerste instantie niet echt een rol. Pas later, als het over de buitenkant en de integratie van details gaat, worden de verschillen duidelijk. Koolstofvezel brengt het design naar een heel nieuw niveau. Beperkingen zoals indrukdiepte spelen opeens geen rol meer. En dat betekent dat designers veel spectaculairdere oppervlaktes kunnen creëren – of vlakkere als ze dat liever willen.
"Als we staal hadden gebruikt, was de motorkap veel minder indrukwekkend geweest dan die nu is. We hebben de auto nu meer kunnen beeldhouwen, met scherpere hoeken op de kenmerkende lijnen. Daardoor ziet de auto er technischer en verfijnder uit", voegt Zef eraan toe.
Hij vervolgt: "Met koolstofvezel in een kleinschalige productie kun je veel met de hand doen. Dus kun je altijd een oplossing vinden, je kunt met de leverancier praten en dingen anders doen om het juiste resultaat te bereiken. Verhoudingen en uitstraling zijn in elk ontwerp altijd erg belangrijk en we zijn uiteraard erg blij met het resultaat."
Het spuiten van koolstofvezel is totaal anders dan het spuiten van staal. Om de perfecte kleur en afwerking te bereiken, moest het team alles uit de kast halen.
De buitenkant telt
Dergelijk exclusief en duur materiaal vraagt om expertise en vakmanschap in elke fase van het proces. Voor het spuiten van de nieuwe Polestar 1 is er dan ook veel geëxperimenteerd en geoefend.
"Elke auto-ontwerper weet precies wat hij moet doen – en wat niet – als hij een auto maakt van staal. Maar dit is iets heel anders. Bijna alles is mogelijk", zegt Zef.
Maar het spuiten van koolstofvezel is totaal anders dan het spuiten van staal. Alle onderdelen komen gecoat met een primer bij de leverancier vandaan en om de perfecte kleur en afwerking te bereiken, moest het team alles uit de kast halen.
Hetzelfde geldt voor de kwaliteitscontrole. Waar scherpziende, hooggekwalificeerde mensen vroeger imperfecties in kleur of afwerking moesten opsporen, kwamen die er nu achter dat dergelijke problemen bij koolstofvezel niet bestaan. Ze letten nu op totaal andere kwaliteitsaspecten. Net als bij alles wat Polestar is, ligt ook hier de lat hoog en gaat iedereen voortdurend tot het uiterste om de ideale manier te vinden om met het materiaal te werken.

Als veiligheid onderdeel is van prestaties
Polestar heeft uitgebreide tests uitgevoerd om te kunnen voldoen aan de strenge veiligheids- en duurzaamheidseisen die aan de Polestar 1 worden gesteld. Onderdelen van koolstofvezel assembleren met het stalen chassis en andere onderdelen van de Polestar 1 is een lastige klus. Staal is elastischer dan koolstofvezel en om de twee materialen aan elkaar te verbinden gebruikt Polestar speciaal ontwikkelde lijm die bestand is tegen de bewegingsvariatie van stalen en koolstofvezelonderdelen. Zef licht toe:
"De uitdaging is dat koolstofvezel een lineair breekbaar materiaal is en dat traditionele autostructuren normaal gesproken materialen gebruiken die vervormen voordat ze breken, zoals staal bijvoorbeeld. Koolstofvezel daarentegen gedraagt zich anders, afhankelijk van de richting van de krachten."
Het eindresultaat maakt Polestar 1 tot een auto met wereldwijd toonaangevende eigenschappen op het gebied van botsveiligheid en duurzaamheid. Door de carrosserie van koolstofvezel te combineren met een stalen chassis, biedt de Polestar 1 het beste van twee werelden op het gebied van rijeigenschappen en veiligheid.

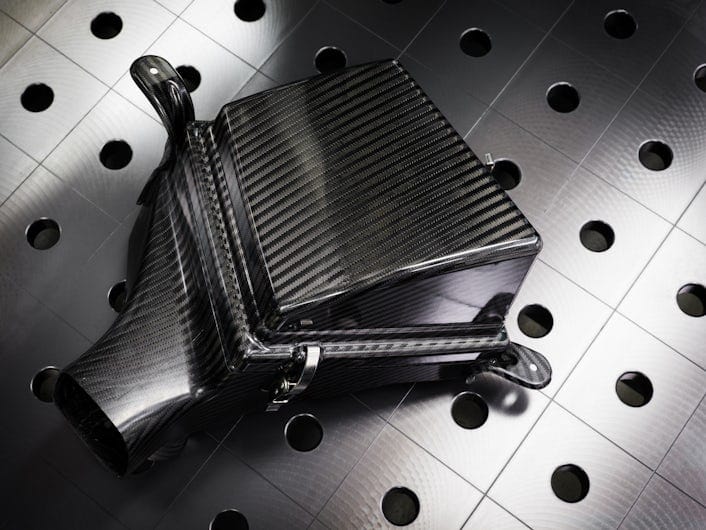
Nadenken over de details
Als we terugkijken op wat we tot nu toe gedaan hebben, is koolstofvezel overtuigend. Het is absoluut high-tech, maar vergt nog steeds een bepaalde hoeveelheid handwerk, plus flink wat geduld om het precies goed te krijgen. Maar als je dat voor elkaar krijgt, ontstaat er een onmiskenbaar gevoel van maatwerk, precisietechniek en geraffineerd design. Je perspectief verandert. Je laat je handen over de auto gaan en je weet dat de buitenkant niet door machines in tools wordt geperst, dat de carbon patches stuk voor stuk met de hand worden aangebracht en dat het patroon daarom klopt. Je weet ook dat elk onderdeel met de hand en met obsessieve precisie wordt afgewerkt. Alles bij elkaar geeft dat je een heel speciaal gevoel.
Elke carbon patch wordt met de hand aangebracht om te zorgen dat het patroon klopt en elk onderdeel wordt ook handmatig afgewerkt.
Zal koolstofvezel in de toekomst vaker worden gebruikt? Die vraag is lastig te beantwoorden en voordat een team tot zo'n keuze komt, moeten er over veel parameters beslissingen worden genomen. Maar één ding is zeker: er zijn veel plaatsen in auto's die bij uitstek geschikt zijn voor toepassing van koolstofvezel en de voordelen zijn het waard. Als het gebruik ervan gangbaarder wordt, dan is het goed om te weten dat leveranciers ook aan het kijken zijn naar manieren om het materiaal in de toekomst te kunnen recyclen en hergebruiken. Een kritische factor in de toepassing van het materiaal in de Polestar 1.
Dus heeft het team de juiste balans gevonden en is het de Polestar-filosofie trouw gebleven: geen concessies, geen gemakzucht?
Het lijkt er wel op… maar dat is nog niet alles.
Koolstofvezel is één van onze geavanceerde technologieën. Er zijn er nog veel meer.
Polestar 1 is een Electric Performance Hybrid, een exclusieve auto die elektrisch rijden combineert met uitstekende prestaties, fraaie verhoudingen, voortreffelijk vakmanschap en innovatieve technologie. Elk onderdeel wordt met zorg ontwikkeld en geselecteerd. Het gebruik van koolstofvezel is slechts één uiting van hoe belangrijk wij het vinden om van Polestar 1 een compromisloze auto te maken.
Weetjes - Koolstofvezel en Polestar 1:
- 1.Gewicht. Een totale besparing van 230 kg dankzij de toepassing van koolstofvezel in combinatie met het SPA-chassis.
- 2.Stijfheid. Verhoogde torsiestijfheid van 22 Nmm-2 tot 32 Nmm-2. Dat is +45%.
- 3.Zwaartepunt. Een stalen SPA-vloer + koolstofvezel carrosserie verlaagt het zwaartepunt en zorgt voor een superieure wegligging en dito prestaties.