Journaal 5
Toen de Polestar 1 vorig jaar aan de wereld werd onthuld, was de reactie overweldigend. Ondanks zijn uiterlijk liet het eerste model van Polestar er geen twijfel over bestaan: dit was geen conceptauto.

De perfecte balans
Dit was een interessante nieuwe auto van een ambitieuze fabrikant. De Polestar 1 is laag, gestroomlijnd en opmerkelijk gespierd. En achter de schermen was iedereen bij Polestar ervan overtuigd dat je die fraaie proporties in 2019 zou terugzien in de allereerste productieversie.
Maar om trouw te blijven aan het oorspronkelijke ontwerp, zou Polestar geavanceerde materialen moeten gebruiken. Carbon zou nodig zijn om de ranke lijnen te behouden en het gewicht te beperken. Bovendien zou Polestar daarmee zijn ambitieuze prestatiedoelen kunnen halen.
Maar welke uitdagingen zou het materiaal uiteindelijk met zich meebrengen? Zouden de designers en ingenieurs de juiste balans kunnen vinden? En zouden de voordelen van carbon echt de moeite waard zijn?
We spraken met Zef van der Putten, Principal Engineer voor de Polestar 1, om daarachter te komen.

Het gebruik van carbon perfectioneren
Carbon wordt nog steeds beschouwd als een exclusief en duur materiaal. Maar door zijn lage gewicht is het de perfecte keuze voor een auto die zo veel geavanceerde technologie, futurisme en prestaties garandeert.
Zo'n dertig jaar geleden werd carbon voor het eerst gebruikt in de Formule 1. Het was lastig om mee te werken, maar wie het lukte, profiteerde van enorme voordelen. Het was namelijk veel lichter en sterker dan andere materialen. Algauw werd het door alle Formule 1-teams gebruikt. Daarna volgden de fabrikanten van dure performance-auto's. De reputatie van carbon als belangrijke prestatieverbeteraar was daarmee bezegeld.
Als we een sprong vooruit maken, zien we dat carbon carrosserieën tegenwoordig de belichaming van technologisch geavanceerde prestaties zijn geworden: ze verlagen het gewicht, verhogen de prestaties, verlagen het zwaartepunt en verbeteren de torsiestijfheid van de auto.
Dit wordt bevestigd wanneer we de auto van dichtbij bekijken. Technisch gezien is het een echt raspaardje. De bovenste helft van de carrosserie, inclusief de portieren, de voorspatborden, de motorkap en het kofferdeksel, zijn gemaakt van Carbon-Fibre Reinforced Polymer (CFRP). En dan is er nog die lage daklijn die zo veel mensen fascineert.
"Met een gewone stalen dakconstructie zouden al deze onderdelen groter zijn geweest. Het dak zou hoger zijn en de ramen zouden meer rechtop staan. Door de hele dakconstructie van carbon te maken, konden we die lage, sierlijke daklijn realiseren", zegt Zef.
De libelle (orde der Anisoptera): de natuurlijke oplossing voor kracht en wendbaarheid. Geperfectioneerd door voortdurende evolutie.
Het oog volgt automatisch de lijn van de A-stijl naar de C-stijl. Maar wat eronder zit, blijft onzichtbaar: een ultrastijve prefabbuis van carbon die geïntegreerd is in de twee halve panelen van de carbon dakstijlconstructie. Ze zijn horizontaal met elkaar verbonden door platte, lichte en ultrastijve dwarsbalken van carbon.
Maar ook het SPA-platform is sterk aangepast. Zo is de wielbasis met 320 mm en de achterkant met 200 mm verkort. Zoals alle goede ingenieurs heeft het team daarna inspiratie gezocht in de natuur en de Dragonfly* verwerkt in de constructie. Dat is een stuk carbon in de vorm van een insect dat met het chassis is verlijmd. De 'vleugels' en 'buik' verbeteren de torsiestijfheid op een van de kritieke punten in de carrosserie, namelijk het gedeelte tussen de middenvloer en de achterconstructie. Het resultaat is spectaculair: de torsiestijfheid van het chassis is met 45% toegenomen.
*Een slim gevormd stuk CFRP dat met de stalen voertuigbodem is verlijmd, verstevigt de vanouds zwakke verbinding tussen de middenvloer en de achterconstructie. Bij Polestar wordt dit onderdeel de Dragonfly genoemd.
Binding met het materiaal
Toen we hem vroegen hoe hij het vond om met carbon te werken in het project, antwoordde Zef:
"Een van de grootste uitdagingen was om het materiaal te leren kennen. We wilden de perfecte oplossing voor de Polestar 1 en waren bereid om die koste wat het kost te vinden. We hebben veel geleerd en hoewel niet alles ging zoals we hadden verwacht, waren de verrassingen juist heel leerzaam. Het proces heeft geleid tot een zeer hoog precisie- en afwerkingsniveau."
Toen ze eenmaal vertrouwd waren met het materiaal, gingen de Polestar-ingenieurs aan de slag om alle andere parameters te definiëren en controleren. Daarvoor moesten ze onder andere beslissen welk type vezel en hars ze zouden gebruiken en hoe ze de diverse delen zouden assembleren en lakken.
De ingenieurs leerden ook om het materiaal te definiëren voor CAE-berekeningen (Computer Aided Engineering), zodat ze de onderdelen konden testen en evalueren. Uit ervaring wisten ze dat carbon op de richtingskrachten reageert. Daarom werden er simulaties gedaan om te voorspellen hoe het materiaal zich in de praktijk zou gedragen.
En deze slimme modellen hadden wel degelijk nut. Het materiaal is nu in bepaalde weefrichtingen in de auto geplaatst, zodat krachten worden opgevangen en de sterkte onder verschillende rijomstandigheden wordt vergroot.
We hadden hoge verwachtingen van de prestaties en lage verwachtingen van de afmetingen en het gewicht van de auto. Tijdens het proces hebben we dus veel onderzocht, geanalyseerd, getest en ook een beetje gepuzzeld. Door het materiaal in de voertuigbodem te integreren, is het extra gewicht van de accu's volledig tenietgedaan. Daardoor is de auto maar liefst 230 kg lichter.
Indrukwekkend.
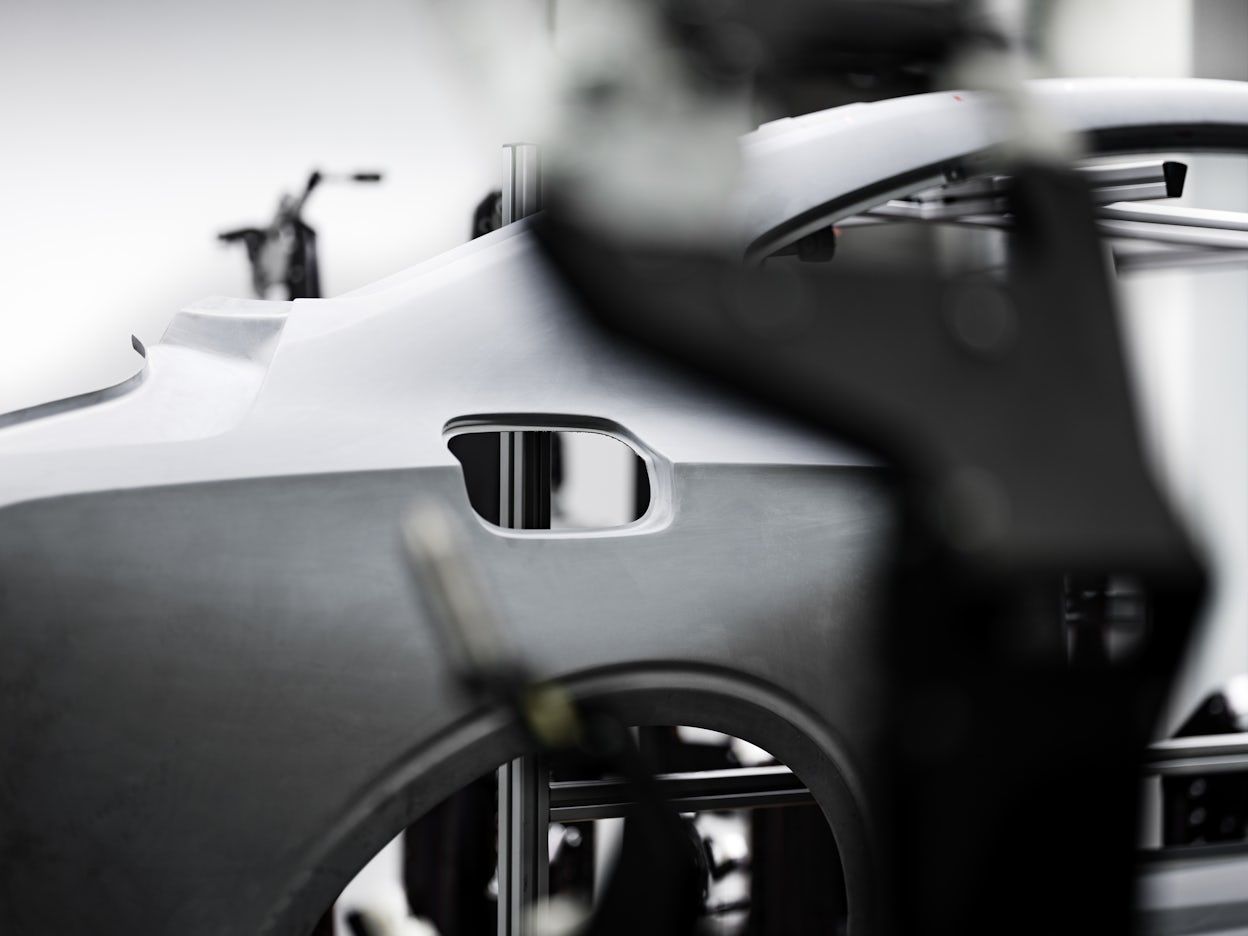
Totstandkoming van het design
Designconcept en uitvoering zijn cruciaal binnen de auto-industrie. Dat geldt voor elk merk. Omdat de Polestar 1 als eerste model uit de Polestar-stal kwam, wilden we echt een statement maken en de designtaal van het merk visualiseren.
Volgens Zef speelt het materiaal in eerste instantie geen grote rol. Pas later, wanneer het tijd is voor de oppervlakken en details, worden de verschillen duidelijk. Met carbon krijgt het design een compleet nieuwe dimensie. Beperkingen, zoals de persdiepte, zijn opeens geen probleem meer. Dat betekent dat de designers veel spectaculairdere oppervlakken kunnen creëren. Of plattere, als ze dat willen.
"Als we met staal hadden gewerkt, zou de motorkap een veel minder spectaculair oppervlak hebben. Nu konden we de auto meer als een sculptuur benaderen en scherpere randen geven aan de kenmerkende lijnen. Daardoor ziet de auto er technischer en verfijnder uit", zegt Zef.
"Wanneer je carbon in kleine aantallen produceert, kan er veel handmatig worden gedaan. Je kunt dus altijd oplossingen vinden, met de leverancier praten en dingen anders doen om het juiste resultaat te bereiken. De proporties en postuur zijn altijd belangrijke designelementen en we zijn natuurlijk heel blij met het resultaat."
Carbon is een totaal ander materiaal om te lakken dan staal. Om de juiste kleur en afwerking te krijgen, werd het team uitgedaagd om naar perfectie te streven.
Wat telt, is de buitenkant
Voor een materiaal dat zo exclusief en duur is, zijn deskundigheid en vakmanschap vereist in alle fasen van het proces. En er is veel geëxperimenteerd en geoefend om de nieuwe Polestar 1 te lakken.
"Iedere autodesigner weet precies wat hij wel en niet moet doen wanneer hij een auto in staal ontwerpt. Maar dit is iets heel anders. Bijna alles is mogelijk", zegt Zef.
Maar carbon is een totaal ander materiaal om te lakken dan staal. Alle onderdelen worden geleverd met een laag grondverf en om de juiste kleur en afwerking te krijgen, moest het team worden uitgedaagd om naar perfectie te streven.
Dat geldt ook voor de kwaliteitscontrole. Vakmensen die ooit met haviksogen naar de kleinste onvolmaaktheden in kleur of afwerking speurden, kwamen erachter dat die problemen niet bestonden in gelakt carbon. Ze zoeken nu naar compleet andere kwaliteitsgebreken. Zoals altijd bij Polestar ligt de lat hoog en iedereen is altijd op zoek naar de perfecte manier om met het materiaal te werken.

Veiligheid als onderdeel van de prestaties
Polestar heeft de Polestar 1 uitvoerig getest om te voldoen aan strenge veiligheids- en duurzaamheidseisen. Het is een uitdaging om de onderdelen van carbon te assembleren op het stalen platform en te bevestigen aan de andere onderdelen van de auto. Omdat staal elastischer is dan carbon, gebruikt Polestar een speciaal ontwikkelde lijm om de twee materialen met elkaar te verbinden. Deze lijm kan het verschil in beweging tussen staal en carbon opvangen. Zef legt uit hoe dat werkt:
"Het probleem is dat carbon in de lengterichting kan breken, terwijl voor traditionele autoconstructies meestal materialen worden gebruikt die eerst vervormen en dan breken, zoals staal. Maar afhankelijk van de richting van de krachten reageert carbon op verschillende manieren."
Wat betreft botsveiligheid en duurzaamheid, is de Polestar 1 uiteindelijk een van de beste auto's ter wereld geworden. Door de combinatie van carbon voor de carrosserie en staal voor het platform biedt de Polestar 1 het beste van twee werelden in termen van rijeigenschappen en veiligheid.

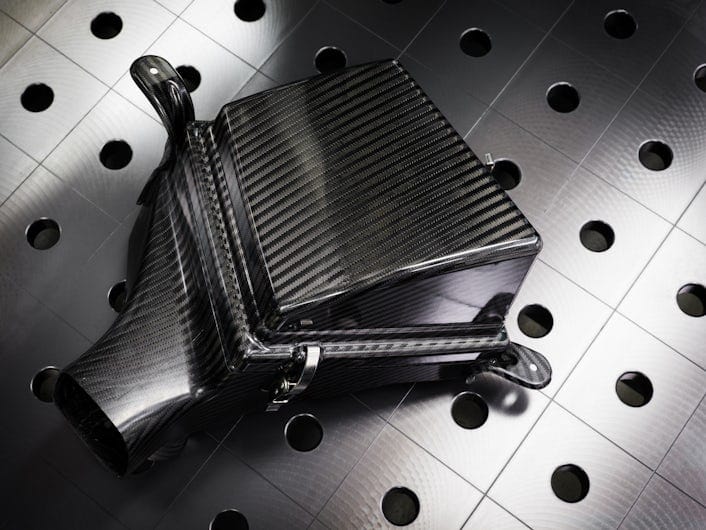
Nadenken over de details
Terugkijkend op het werk tot nu toe valt er veel te zeggen voor carbon. Het materiaal is beslist hightech en vereist nog veel vakmanschap. Bovendien is er heel wat geduld nodig om een perfect resultaat te bereiken. Maar het gevoel van precisietechniek en hoogwaardig design dat daardoor wordt opgeroepen, valt onmogelijk te ontkennen. Je krijgt een andere kijk op de auto. Wie zijn handen eroverheen laat glijden, beseft dat de oppervlakken niet door machines in mallen zijn geperst, maar dat elk stuk carbon met de hand is aangebracht. De patroonlijnen sluiten daardoor perfect op elkaar aan. Elk onderdeel is handmatig en haast overdreven nauwkeurig afgewerkt. Alles bij elkaar geeft dat een heel bijzonder gevoel.
Elk stuk carbon wordt met de hand aangebracht, zodat de patroonlijnen perfect op elkaar aansluiten. Elk onderdeel wordt bovendien handmatig afgewerkt.
Zal carbon in de toekomst vaker worden gebruikt? Dat is een lastige vraag, want voordat een team die beslissing kan nemen, moet het rekening houden met tal van parameters. Maar één ding is zeker: heel veel plekken in een auto zijn perfect geschikt voor carbon en de voordelen zijn beslist de moeite waard. De leveranciers onderzoeken ook hoe ze het materiaal in de toekomst kunnen recyclen en hergebruiken als de toepassing ervan normaal wordt. Dat is goed om te weten, want voor de Polestar 1 is dat een essentiële voorwaarde.
Is het dus gelukt om de juiste balans te vinden en trouw te blijven aan de Polestar-filosofie? Geen compromissen? Geen besparingen?
Het lijkt er wel op … en meer dan dat.
Carbon is een van onze geavanceerde technologieën. Maar er zijn er nog veel meer.
De exclusieve Polestar 1 is een elektrische performance-hybride, die een elektrische aandrijving combineert met voortreffelijke prestaties, schitterende proporties, uitstekend vakmanschap en innovatieve technologie. Elk onderdeel is met zorg ontwikkeld en gekozen. Het gebruik van carbon is slechts één voorbeeld dat laat zien hoe belangrijk we het vinden om geen concessies te doen bij de bouw van de Polestar 1.
Snelle feiten over carbon in de Polestar 1:
- 1.Gewicht. Het gebruik van carbon in combinatie met het SPA-chassis bespaart in totaal 230 kg aan gewicht.
- 2.Stijfheid. De torsiestijfheid neemt toe van 22 Nmm-2 tot 32 Nmm-2 en ligt daarmee 45% hoger.
- 3.Zwaartepunt. De stalen SPA-vloer en bovenkant van carbon verlagen het zwaartepunt voor superieure rijeigenschappen en prestaties.